Rigaku SmartSite RS Portable Stress Analyser
The SmartSite RS combines patented technology with the latest generation electronics, the highest performance in a rugged, portable multipurpose instrument that can be used to determine:
- Residual stress
- Retained Austenite (with option PSD attachment)
- Hardness estimation from width of diffraction peak
While having been designed for in field applications, the SmartSite RS is equally at home in a lab, where it can be coupled with a shielded enclosure or instrument cart.
This system benefits from Rigakus long history in the X-ray business and the many technologies that they have developed and refines over the years. These benefits translate into a high performance, user-friendly, reliable instrument that you can trust.
High flux X-ray tube + Fast 2D detector = Ultimate Performance
Key Features
- Uses original DRS technology (patent pending)
- High speed 2D detector
- High flux X-ray source
- Highest speed measurement
- Typical measurement time <60sec
- Wireless operation via tablet PC
- Small-size and lightweight
- No need for mains power or external cooling
- Built-in safety features to protect operator from X-ray exposure
- Simple operation
- Results instantly displayed on the tablet PC screen
Original Stress Analysis Technology
Rigaku have developed DRS (Direct Refinement Solution, patent pending) technology which is unique to the SmartSite RS. The instrument can simultaneously determine the stress-free and stress tensorsg, (d0 and ?ij respectively) and does not rely in external databases. This methodology has been tested and is in strong agreement with measurements performed using more conventional methodologies.
High Speed Detector
The SmartSite RS comes equipped with a high-speed (3ms readout) 2-dimensions semiconductor HPAD detector (Hybrid Pixel Array Detector), the same technology that is used on Rigakus high end diffractometers. This equates to faster data collection and zero background noise. Data is displayed instantaneously once the exposure time has elapsed. This allows you to complete most common measurements within 60 seconds, with some possible in as little as 10 seconds and enables you to perform dynamic studies.
Most other systems utilise imaging plate detectors which typically take 30 seconds just to collect the data.
X-Ray Tube
The SmartSite RS uses Cr radiation that operates at 50W which offers as much, if not more than any other system on the market (most other systems only provide 30W). This ensures you get excellent penetration and faster results compared to lower powered instruments.
The X-ray tube itself is actually rated to work at much higher power levels which means it is operating well within its capabilities. For the operator, this means stable and reliable performance and long life.
User-Friendly Operation
The SmartSite RS is controlled via table PC. Using a simple touchscreen interface, all measurement parameters can be easily viewed and adjusted. At the completion of the measurement, all data and measurements can be immediately displayed on the same screen providing true in situ measurements.
Alignment is also facilitated by simple onscreen indicators including:
- Instrument to sample distance
- Angle of instrument to sample
- CCD image of sample for zeroing in on the desired point of interest
These factors, combined with the lightweight, small form factor and no need for mains power (battery operated) or external water cooling, make the SmartSite RS an ergonomic and operator-friendly solution capable of more than just calculating residual stress.
The design of the head unit has also been optimised for access into tight areas e.g.:
- Small diameter pipes
- Fillet welds
Safety
Operator safety and possible exposure to X-rays was a primary design consideration for the SmartSite RS. For this reason, Rigaku equipped the system with a laser displacement sensor and accelerometer. These ensure that the instrument remains safely and stably in position to carry out a measurement. If the instrument goes outside design tolerances (distance, tilt and vibration), the X-rays will turn off or will simply not come one, thus protecting the operator for potential exposure.
Wireless/Remote Operation
The SmartSite RS portable stress analyser can be operated remotely via tablet PC with a Wi-Fi communications link. This is of particular interest for applications where operators may be exposed to harmful environments.
Applications
Residual stress analysis, as well as hardness and retrained austenite determination is relevant to many industry areas including:
- Automotive e.g. crankshafts, cam shafts, suspension springs, gears, welds in exhaust systems, conrods, chassis, etc.
- Civil engineering e.g. bridges
- Railway e.g. fabricated components
- Heat treatment e.g. after quenching, annealing, induction hardening, carburising etc.
- Oil and gas e.g. pipelines
- Weld joints e.g. to check HAZ
- Metal fabrication e.g. to check parts after forming via processes such as shot peening, casting, extrusion, machining, grinding
- Quality control
- Asset management and maintenance of plant and infrastructure e.g. to monitor stress corrosion cracking (SCC) or hydrogen induced cracking (HIC)
Retained Austenite Determination
Using the optional PSD attachment, the SmartSite RS allows the user to simultaneously measure retained austenite (RA) and residual stress. This option is of specific interest to heat treaters, where controlling the volume % of remaining austenite in the metal components is critical to their performance and longevity.
Formation of Austenite
Metals, such as steel are often heat treated to improve their properties for a given application. Heat treating can improve properties such as surface hardness and toughness.
In the heat treatment of carbon steels, the metal is heated up to temperatures above the critical eutectoid temperature and held at that temperature long enough for the transformation into a harder phase to complete i.e. Ferrite (?-iron) to Austenite (?-iron)
They are then rapidly cooled by immersing them into water, oil or other cooling liquids. When the cooling rate is rapid, the austenite undergoes forms martensite. Depending on the cooling rate, ferrite and cementite may also form.
If low-hardenability steels are heat treated, some austenite may be retained in the structure.
The percentage of each of these phases present in the final structure will determine the mechanical properties of the final component such as hardness, ductility, toughness, impact and tensile strength.
Why is Retained Austenite a Problem
Austenite is stable at high temperatures. If frozen in by quenching, it is considered metastable at room temperature. Under the right conditions, metastable austenite will transform into martensite. This phase transformation brings with it a volumetric change, which induces internal stresses, which if severe enough will result in cracking.
Retained Austenite in Components
Retained austenite is not always a problem. Martensite is strong, very hard yet brittle. Austenite on the other hand is soft, but tough. By controlling the relative amounts of martensite and austenite in the structure, the properties of the metal can be tailored to suit a given application.
For tools and dies, the soft nature of austenite makes it undesirable as they are after wear resistance and dimensional stability.
Gear and bearing manufacturers require toughness which requires the presence of some RA, typically in the volume % range 5 to 30 in the final structure.
Determination of Retained Austenite Using the SmartSite RS
The SmartSite RS is able to determine the volume % of retained austenite directly and quickly.
![]() | ![]() |
?-iron (martensite/ferrite) profile left acquitted using 2D detector (left)
?-iron (austenite) profile acquired using PSD attachment (right)
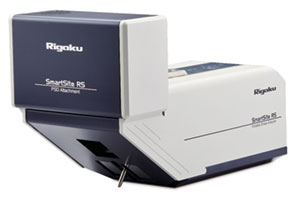
Hardness Measurements
Determination of hardness traditionally involves pushing an indenter into the surface of a materials and measuring the characteristics of the resultant cavity. While classed as non-destructive testing, these indentations may be undesirable e.g. in the case of testing the hardness of the faces of camshaft lobes.
Using the SmartSite RS, you can predict the hardness of a sample in a truly non-destructive manner. The SmartSite RS is a non-contact technique and will not leave any physical sign that a measurement has been taken making it ideal for testing wear faces.
Accessories
The SmartSite RS can also be used for laboratory applications where it can be supplied with:
- Shielded enclosure and/or
- Instrument cart
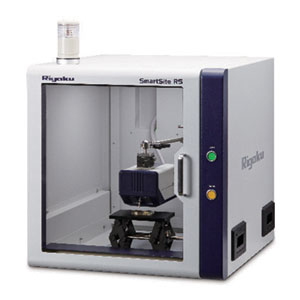
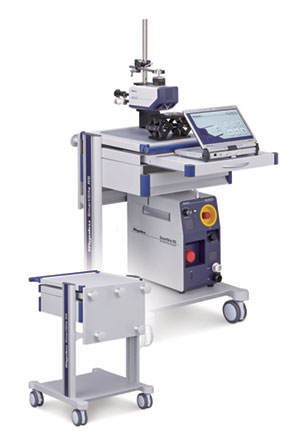
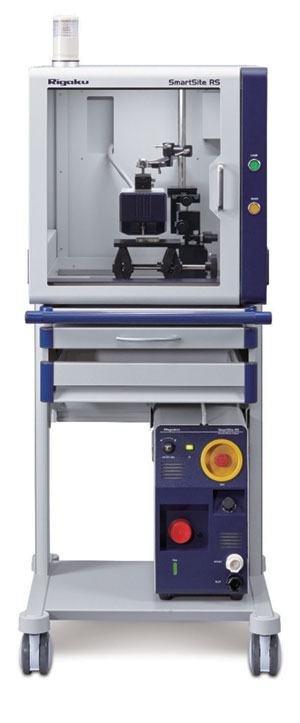