Rigaku NDT (Non-Destructive Testing)
Since its inception in Japan in 1951 Rigaku Corporation has been at the forefront of analytical and industrial instrumentation technology. With hundreds of major innovations to its credit, Rigaku continue to set the standard in x-ray analytical equipment.
Their range of instruments is unmatched and with class leading technologies such as:
- Rotating anode x-ray sources
- Truly self-aligning diffractometers
- Fastest detectors on the market (HyPix and Pilatus)
- Highest power systems
Furthermore, Rigaku also supply multi-layer crystals to other x-ray manufacturers, without which they would not be able to compete in the marketplace. With these crystals being developed in-house, Rigaku continue to lead the field.
Non-Destructive Testing – NDT
Non-Destructive Testing (NDT) procedures are used to inspect components and structures for defects, abnormalities, pores, cracks and other structural imperfections. These inspections may take place as part of the manufacturing process (quality control) or in-service testing where it can be used to prevent premature failure.
As the name suggests non-destructive testing does not damage the specimen and as such, the part can be used, or continued to be used for the purpose that it was intended with no compromise to its service life as a result of the testing performed.
NDT may be carried out in laboratories or in the field. Examples of situations where NDT is a commonly used procedure include:
- Weld testing
- Metal and ceramic castings
- Buildings
- Railways
- Aircraft
- Bridges
- Pipelines
- Industrial components
- Automotive components in particular in motor racing
Rigaku Radiographic NDT Solutions
With a long and strong history in x-ray technology, it is not surprising that Rigaku NDT manufacture some of the world’s best radiographic NDT equipment.
Rigaku specialise in radiographic generator sets producing both pulsed power and constant potential systems. They also have compact systems designed to work in confined spaces.
With Rigaku’s ever evolving technological improvements, combined with their reliability, you can be sure that the instrument you choose will include the most up to date technology and will serve you well into the future.
LMATS Use Rigaku Tube Heads to Prevent Premature Failure
LMATS is a comprehensive provider of testing services with four operations in Australia spread over Victoria, New South Wales and Queensland. One of the areas that they specialise in is Non-Destructive Testing (NDT) of metallic and alloy parts for failure investigation and component verification. Amongst their clients are BAE Systems – Australia (Australian Navy and Military) as well as automotive manufacturers such as General Motors.
They employ a range of NDT testing technologies to carry out investigations. One of the technologies they rely heavily on is radiographic testing. They use this to evaluate pipes, plates, castings, weld joints and other structural components in steel, aluminium and other alloys. These types of parts and structures are used in industries such as automotive, power generation and pressure vessels. Some of the components that they test are critical to the operations that they are employed in. Ensuring they pass quality control tests before being installed and premature failure may be detected before it happens are both of the utmost importance.
To perform the bulk of their testing in Melbourne, LMATS use a Rigaku 200kV Radioflex tube head. When asked why they use this system, Kevin Eastwood their senior RT technician explained: The 200kV system is light and practical for the applications that we need it for, whether they are in our lab or off on the clients site. The actual unit we use has been in service since 1994. Shes not the prettiest anymore, but she is extremely reliable. In all the time we have had her, shes only ever needed one service and is a workhorse that is constantly in use.
A lot of the work Kevin does is with aluminium structures so he does not need to run the system at full power. Another advantage of the 200kV system is that it only requires a smaller exclusion zone and is easier to contain. This is particularly beneficial when working on site.
Other LMATS offices have higher powered Rigaku Radioflex tube heads (250kV and 300kV). These higher powered units are typically used for testing of pipe welding and welding procedure/qualification testing.
When required, the offices swap units depending on the technical requirements of the jobs. Having a fleet of such similar units also makes it easier for the various operators.
Kevin added: Our 200kV Radioflex unit is certainly getting old, but it performs day in and day out. I have been in the game for over 11 years and have worked with other Rigaku units in the past and have also found their reliability to be outstanding. One day when this unit is retired, we will certainly look at replacing it with a newer Rigaku system.
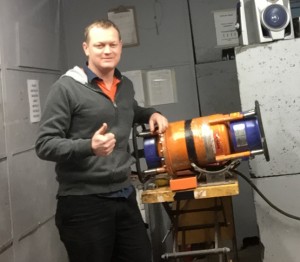
Kevin Eastwood from LMATS with a Rigaku Radioflex tube head.
